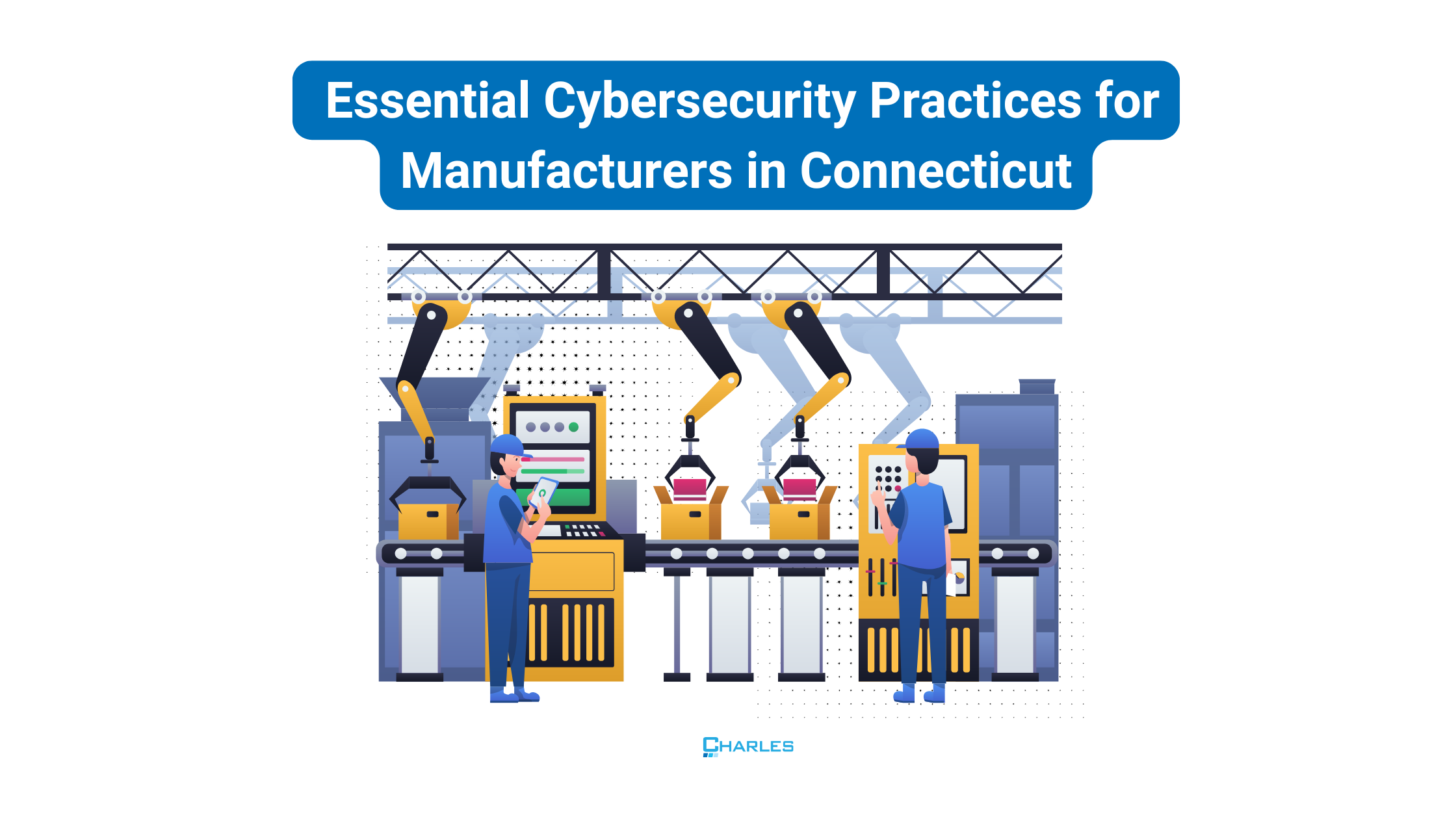
Introduction: The Cybersecurity Landscape for Connecticut Manufacturers
Cybersecurity is critical for Connecticut’s manufacturing industry, which is increasingly facing cyber threats that can disrupt operations, steal intellectual property, and compromise sensitive data. This is especially important for manufacturers working with the Department of Defense (DoD), as they must comply with the recently published Cybersecurity Maturity Model Certification (CMMC) 2.0 rule. Officially released on October 15 and set to take effect on December 16, CMMC 2.0 mandates cybersecurity standards for handling Federal Contract Information (FCI) and Controlled Unclassified Information (CUI). This regulation highlights the heightened cybersecurity expectations for manufacturers in defense, as well as the need for cybersecurity across the entire industry.
Connecticut manufacturers encounter unique challenges, including managing both legacy and modern technologies, complex supply chains, and limited cybersecurity resources. These factors make it essential to adopt cybersecurity practices that not only strengthen defenses but also help maintain compliance with evolving standards. In this blog, we’ll explore key practices to help Connecticut manufacturers protect their operations, safeguard critical data, and build a secure environment.
Understanding Cyber Threats Facing Manufacturers
As manufacturing becomes increasingly digitized, the sector has also become one of the top targets for cybercriminals. According to the World Economic Forum, “Heightened connectivity and data transparency has made manufacturing the most targeted sector for cyberattacks for three years in a row.” The sector now accounts for 25.7% of all cyberattacks, with ransomware involved in 71% of these incidents. Manufacturing organizations are particularly vulnerable to ransomware attacks due to their limited tolerance for downtime and relatively low cybersecurity maturity compared to other industries.
Recent cyberattacks in Connecticut emphasize these vulnerabilities, with multiple industries facing significant disruptions in the fall of 2023. In one of the state’s largest recent breaches, a file transfer software vulnerability involving "MOVEit" compromised sensitive data for hundreds of thousands of Connecticut residents.
“It’s one of the biggest that we have seen recently,” said Robin Chataut, assistant professor of cybersecurity and computer science at Quinnipiac University, in an interview with Fox61.
The incident highlights the risk of cyber threats to Connecticut’s manufacturers and the potential impacts on their operations and reputation. Common threats that manufacturers face include:
-
Ransomware: Attackers encrypt critical data and demand payment, capitalizing on the industry’s low tolerance for downtime.
-
Phishing: Cybercriminals trick employees into revealing sensitive information, often through fraudulent emails or messages.
-
Supply Chain Attacks: Hackers infiltrate via trusted third-party vendors, compromising sensitive data and disrupting operations across the supply chain.
Fortunately, there are ways that manufacturing organizations can protect themselves.
Practice #1: Employee Training and Awareness
Manufacturing employees are trained to stay safe in the facility—whether it’s wearing a hard hat, staying within designated areas, or watching their step. Equally essential is cybersecurity training, which allows employees to serve as the first line of defense against costly cyber incidents. Through cybersecurity awareness training, employees learn to recognize potential hazards such as phishing emails, follow best practices for protecting information, and know how to report suspicious activity.
Recommended training programs should emphasize awareness, education, and reporting. Leaders should also clearly communicate cybersecurity policies, so everyone understands their role. Awareness of the risks and potential impact of cyber threats helps everyone remain vigilant. Many managed service providers (MSPs) offer such programs. For instance, Charles IT provides cybersecurity awareness training specifically tailored for manufacturers.
Practice #2: Securing IoT Devices and Industrial Control Systems
In the manufacturing industry, Internet of Things (IoT) devices and Industrial Control Systems (ICS) play critical roles in improving efficiency and automating processes. IoT devices are connected equipment like sensors, cameras, or monitors that collect and transmit data to improve processes. Industrial Control Systems are technology solutions that help monitor and manage machinery and equipment in real-time, often controlling key manufacturing functions such as production, assembly, and distribution. While these connected devices and systems boost productivity, they also create new cybersecurity risks. If they’re left unprotected, they can serve as easy entry points for cybercriminals, potentially resulting in data breaches, system downtime, or even full operational shutdowns.
To secure IoT and ICS environments, here are three essential best practices:
-
Segment Network Access: Keep IoT and ICS devices on separate network segments from regular business operations. This limits exposure and makes it harder for attackers to move through the network if one area is compromised.
-
Regularly Update and Patch Devices:
Ensure all connected devices and control systems are updated with the latest security patches to protect against known vulnerabilities.
-
Implement Strong Authentication and Access Controls: Restrict access to IoT and ICS devices to only those who need it and require multi-factor authentication to prevent unauthorized access.
Practice #3: Regular Software Updates and Patch Management
While we touched on the importance of updates for IoT devices, regular software updates and effective patch management deserve their own spotlight. Keeping all software and systems up to date is critical for more than just security, although patching vulnerabilities does play a major role in preventing cybercriminals from infiltrating networks. Timely updates also improve system performance and stability, reducing the risk of costly downtime that can arise if critical systems fail or are breached.
To implement effective patch management protocols, consider these strategies:
-
Create a Patch Management Schedule: Establish a regular schedule for assessing and applying patches, prioritizing updates that address known security vulnerabilities.
-
Test Patches Before Deployment: Test new patches in a controlled environment before rolling them out network-wide to prevent unexpected issues that could disrupt operations.
-
Automate Where Possible: Use automated tools to manage updates and patches across systems.
Practice #4: Data Protection and Backup Solutions
Modern manufacturing relies on connected systems, automation, and AI to keep operations running smoothly. At the core of these processes is data, which is the information that ensures each part of production works seamlessly with the next. If this data is disrupted or, worse, hacked, it can halt production or expose valuable operational insights to competitors. Manufacturers benefit by focusing on both data security to protect proprietary information from theft and data integrity to ensure products meet the quality and design standards set by engineers.
Best practices for data protection and backup solutions include:
-
Data Encryption: Encrypt data both in transit and at rest to protect sensitive information from unauthorized access.
-
Access Controls: Limit data access to authorized personnel only, ensuring that sensitive information remains secure.
-
Regular Backups: Schedule consistent backups to maintain data availability and allow for quick recovery in case of cyber incidents or data loss.
Practice #5: Developing an Incident Response Plan
Every manufacturer needs a well-defined incident response plan that all employees understand and can follow in the event of a cyberattack. A clear, practiced plan ensures that if cybercriminals infiltrate systems, employees will know their roles in responding and mitigating the impact. This not only reduces the potential damage to operations but also speeds up recovery, helping the business resume normal activities faster.
Key components of an incident response plan include:
-
Identification and Reporting: Recognize potential threats quickly and report them promptly, allowing for a swift initial response.
-
Response and Mitigation: Take immediate actions to contain the threat, reduce its impact, and safeguard critical systems to minimize downtime.
-
Eradication and Recovery: Remove all traces of the threat from affected systems and work to restore data and operations to full functionality.
To ensure that an incident response plan is effective, manufacturers can conduct tabletop exercises with their managed service provider (MSP). These exercises simulate a cyber incident, allowing teams to practice their roles and identify areas for improvement. This hands-on approach reinforces employee readiness and highlights any adjustments needed for a real response.
Practice #6: Compliance with Industry Regulations
For manufacturers in Connecticut and across the U.S., two key cybersecurity regulations are essential: the Cybersecurity Maturity Model Certification (CMMC) 2.0 and the Defense Federal Acquisition Regulation Supplement (DFARS). CMMC 2.0 establishes data security requirements for contractors working with the U.S. Department of Defense (DoD), mandating that they meet specific levels based on the sensitivity of the data they handle. DFARS, meanwhile, requires all companies working with the DoD to adhere to strict data security standards to secure and maintain contracts.
To ensure compliance, manufacturers can implement the following IT security solutions:
-
Backup and Disaster Recovery: Protects critical data by ensuring it’s regularly backed up and recoverable in case of data loss or cyber incidents.
-
Dark Web Monitoring: Continuously scans the dark web for compromised credentials or sensitive information, helping to mitigate risks of unauthorized access.
-
Endpoint Encryption: Secures sensitive data on devices such as computers and mobile phones, preventing unauthorized access if devices are lost or stolen.
-
External Vulnerability Scanning: Regularly scans for vulnerabilities in external-facing systems to identify and address security gaps.
-
Security Awareness Training: Educates employees on recognizing and responding to cyber threats like phishing attacks, helping to prevent breaches from human error.
-
Security Information and Event Management (SIEM): Provides real-time monitoring and analysis of security events, enabling faster detection and response to potential threats.
By meeting these compliance standards, manufacturers not only strengthen their defenses against cyberattacks but also protect their contracts, avoid potential fines, and uphold a good reputation with customers.
Conclusion: Strengthening Cybersecurity for a Resilient Future
In an increasingly connected manufacturing landscape, Connecticut manufacturers must prioritize essential cybersecurity practices to safeguard their operations. Key strategies include employee training, securing IoT devices and industrial control systems, implementing regular software updates, developing incident response plans, and maintaining compliance with industry regulations. By adopting these measures, manufacturers can create a cybersecurity framework that protects their valuable data and mitigates the risk of cyber threats.
We encourage all manufacturers to take proactive steps in enhancing their cybersecurity posture. Don’t wait for a cyber incident to occur—investing in cybersecurity today is crucial for ensuring the long-term success of your business.
At Charles IT, we specialize in providing tailored cybersecurity solutions to meet the unique needs of manufacturers. Reach out to us today to learn how we can help you strengthen your cybersecurity!