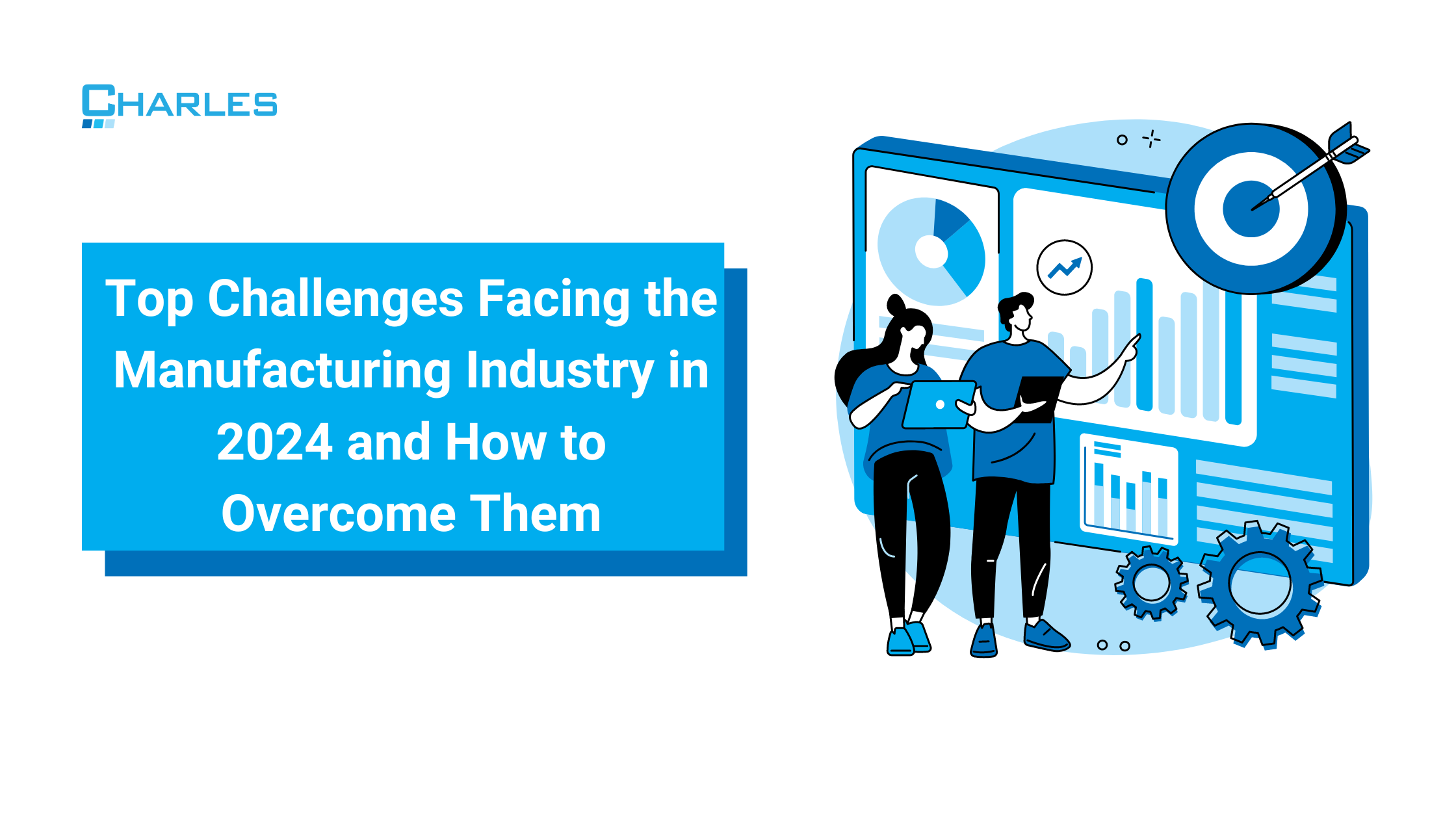
Introduction: Navigating the Manufacturing Landscape in 2024
For decades, the manufacturing industry has remained a cornerstone of the global economy since it provides essential goods and products that power everyday life. However, this sector is still not without its challenges, particularly due to the evolving business landscape of 2024. That’s because reports suggest that manufacturers must stay competitive while adapting to the rise of automated technologies, including AI. In addition to that, they face hurdles such as supply chain disruptions, labor shortages, rising material costs due to inflation, and ever-changing regulatory requirements.
Despite these obstacles, manufacturers can position themselves for success by identifying and addressing these issues head-on, especially through the strategic use of technology. In this blog, we’ll explore key challenges such as supply chain instability, workforce shortages, increased operational costs, digital transformation, and regulatory compliance, along with practical solutions to help manufacturers thrive in 2024 and beyond.
Challenge #1: Supply Chain Disruptions
Supply chain disruptions are one of the most significant challenges manufacturers face, as they often stem from factors beyond their control. In fact, the National Association of Manufacturers’ 2023 “Manufacturers Outlook Survey” found that 37.8% of the manufacturers that they surveyed believed it to be a top challenge. A variety of issues can lead to disruptions, with transportation and logistics being major contributors. Delays can occur due to traffic, shipping damage, or severe weather events like hurricanes, tornadoes, or floods. These natural disasters can halt operations entirely, creating bottlenecks in the delivery of critical materials.
Beyond environmental factors, man-made disruptions also pose risks. These can range from extreme incidents, such as fires or warehouse explosions, to seemingly minor mistakes like human error, which can have cascading effects throughout the supply chain. Geopolitical instability is another critical factor, as global political events—including trade conflicts, sanctions, or regional unrest—can interrupt the steady flow of goods and materials.
Solutions: Building Resilient Supplier Networks and Leveraging Technology
To combat these challenges, manufacturers must focus on building resilient supply chains and leveraging advanced technology. Strengthening relationships with key suppliers can ensure priority access to essential materials during shortages or disruptions. Additionally, diversifying the supplier base is crucial so that if one supplier is affected, others can step in to fill the gap.
In terms of technology, manufacturers should implement advanced supply chain management systems that provide real-time visibility into inventory, shipment tracking, and potential disruptions. Predictive analytics and artificial intelligence (AI) can help identify risks before they occur, allowing manufacturers to take proactive measures. Furthermore, automation and Internet of Things (IoT) solutions can optimize operations, helping manufacturers react quickly and efficiently when disruptions arise.
Challenge #2: Labor Shortages and Workforce Skills Gaps
Another significant challenge for manufacturers in 2024 is the ongoing labor shortage and the impact of workforce skills gaps. The issue was already flagged as a major concern in the 2023 Manufacturers' Outlook Survey, where an overwhelming 72.1% of respondents identified retaining a quality workforce as their top challenge. This labor shortage could be driven by national trends such as a shrinking labor pool and increasing competition for skilled workers across industries.
Several factors contribute to the shortage of skilled labor in manufacturing. One of the most pressing is an aging workforce, with many experienced workers retiring without enough younger talent to replace them. At the same time, the rapid pace of technological advancements has left many workers struggling to keep up. The integration of new technologies, including automation and AI, demands a workforce with the technical skills to operate these systems—skills that many current employees may lack.
Solutions: Upskilling Workers and Automating Repetitive Tasks
Fortunately, manufacturers can address these challenges through upskilling and automation. Upskilling refers to training existing workers to expand their knowledge and adapt to new technologies. This can be achieved by implementing training programs, offering certifications, and providing incentives such as wage increases or enhanced benefits to encourage ongoing skill development. This not only helps retain employees but also makes manufacturing companies more attractive to prospective hires.
Recruiting new talent can also be improved by establishing partnerships with educational institutions. Collaborating with schools, colleges, or vocational programs to create internships or specialized training programs can help manufacturers recruit skilled workers early in their careers. These partnerships allow companies to train workers from the start, ensuring they are equipped with the necessary skills and can grow with the organization.
In terms of automation, manufacturers can streamline operations without replacing jobs. The goal is not to have AI take over, but rather to use technology to automate routine, repetitive tasks. This frees up employees to focus on work that requires creativity, problem-solving, and decision-making. By leveraging technology in this way, manufacturers can increase productivity, which would alleviate the strain caused by labor shortages.
Challenge #3: Rising Operational Costs
Rising operational costs, driven by inflation and the increased price of raw materials, are a major challenge for manufacturers. In the 2023 Manufacturer Outlook Survey, nearly half of manufacturers indicated that higher raw material costs were a significant burden on their operations. Inflation, which refers to the general increase in prices across the economy, erodes the purchasing power of money, making it more expensive to buy essential materials, pay for energy, and manage overhead. As a result, manufacturers are often forced to either raise their prices or find ways to reduce costs in order to maintain profitability.
The impact of inflation on manufacturing goes beyond raw materials. It affects everything from energy and labor costs to transportation and logistics. Manufacturers must balance the need to remain competitive while dealing with tighter margins and higher operational expenses.
Solutions: Energy Efficiency, Lean Manufacturing, and Cost-Saving Technologies
One effective way to reduce operational costs is by investing in energy-efficient technologies. Optimizing energy usage—whether through upgrading machinery, using renewable energy sources, or improving building insulation—can lead to cost savings in the long run. By lowering energy consumption, manufacturers can mitigate the impact of rising utility costs.
Implementing lean manufacturing principles also helps eliminate waste and improve efficiency throughout production processes. By streamlining operations, reducing excess inventory, and optimizing workflows, manufacturers can cut unnecessary costs and improve output without compromising quality. Lean methodologies focus on continuous improvement, enabling manufacturers to better adapt to fluctuating costs and market conditions.
Leveraging technology, such as automation, AI, and data analytics, is another solution for manufacturers to combat rising operational expenses. Automating repetitive tasks and using data analytics to optimize production processes can reduce labor costs and increase productivity. Predictive maintenance technologies, for example, can help prevent costly downtime by identifying equipment issues before they break down.
Challenge #4: Adopting Digital Transformation
The growing importance of smart manufacturing and Industry 4.0 technologies presents both opportunities and challenges for manufacturers. While technology offers solutions to many of the issues manufacturers face, adapting to the rapid pace of digital transformation can be difficult. This brings us to the next major challenge: successfully adopting smart manufacturing and Industry 4.0 technologies.
For those unfamiliar, smart manufacturing and Industry 4.0 refer to the digital revolution that is transforming the way businesses produce and distribute goods. These terms encompass the use of advanced technologies like automation, the Internet of Things (IoT), and data analytics to enhance manufacturing processes. The shift to a digital-first approach is reshaping everything from supply chain management to production efficiency and product quality. However, adopting these technologies can be daunting, requiring significant investment, training, and cultural shifts within organizations.
Solutions: Implementing IoT, Automation, and Data-Driven Insights
The solution to this challenge is clear: manufacturers need to embrace digital transformation and incorporate these technologies into their daily operations. The benefits far outweigh the initial challenges, as digital tools can improve efficiency, reduce costs, and increase competitiveness.
Implementing IoT devices for example, enables real-time monitoring of equipment, inventory, and production processes. IoT sensors can provide valuable data on machine performance, enabling predictive maintenance and minimizing downtime.
There are also automation technologies that allow manufacturers to streamline operations by handling repetitive or labor-intensive tasks. This increases efficiency, reduces human error, and allows workers to focus on more complex, value-added tasks.
Finally, by utilizing data analytics, manufacturers can make informed decisions based on real-time information. This helps optimize production processes, improve product quality, and identify potential bottlenecks before they become costly problems.
Challenge #5: Meeting Sustainability and Regulatory Requirements
One of the growing challenges for manufacturers is the push for sustainability and the need to comply with new environmental regulations. Environmental compliance now plays a significant role in the manufacturing sector, with laws, standards, and regulations focused on minimizing the environmental impact of industrial operations. These regulations cover a range of areas, including the handling of hazardous materials and waste, managing water and air emissions, and ensuring that production processes do not harm ecosystems.
The challenge for manufacturers lies not only in meeting these complex regulations but also in the potential consequences of non-compliance. Failing to adhere to environmental standards can lead to costly legal penalties, fines, and even operational shutdowns. Beyond financial repercussions, non-compliance can severely damage a manufacturer's reputation, as sustainability has become a key concern for consumers and investors.
Solutions: Investing in Green Technology and Sustainable Practices
Manufacturers can avoid these negative outcomes by investing in green technology and adopting sustainable practices. One step is implementing energy-efficient technologies, such as solar panels, renewable energy sources, or eco-friendly machinery, which can reduce a manufacturer’s carbon footprint. Additionally, upgrading equipment to minimize energy consumption and waste production can lead to long-term cost savings while ensuring compliance with environmental regulations.
Beyond technology, manufacturers should focus on adopting sustainable practices throughout their supply chains. This can include sourcing materials from environmentally responsible suppliers, reducing waste by implementing recycling programs, and optimizing resource use in production.
Many environmental regulations also now require manufacturers to provide detailed reports on their sustainability efforts, emissions, and resource usage. Implementing tracking systems and data analytics tools can help manufacturers stay compliant and demonstrate their commitment to sustainability.
Conclusion: Preparing for Success in 2024
Manufacturers face several key challenges in 2024, including supply chain disruptions, labor shortages, rising operational costs, digital transformation, and meeting sustainability requirements. However, by embracing solutions like automation, green technology, and upskilling, these hurdles can be turned into opportunities for growth.
Partnering with a managed service provider (MSP) like Charles IT can further support manufacturers by implementing advanced technologies, improving efficiency, and ensuring compliance with evolving regulations. With the right strategies, manufacturers can overcome these obstacles and thrive in the years ahead.
Schedule a call with one of our experts today!